- Veröffentlichungsdatum : 05.06.2018
- – Letztes Update : 07.06.2018
- 12 Min -
- 2313 Wörter
- - 14 Bilder
Power on Rubber Tracks
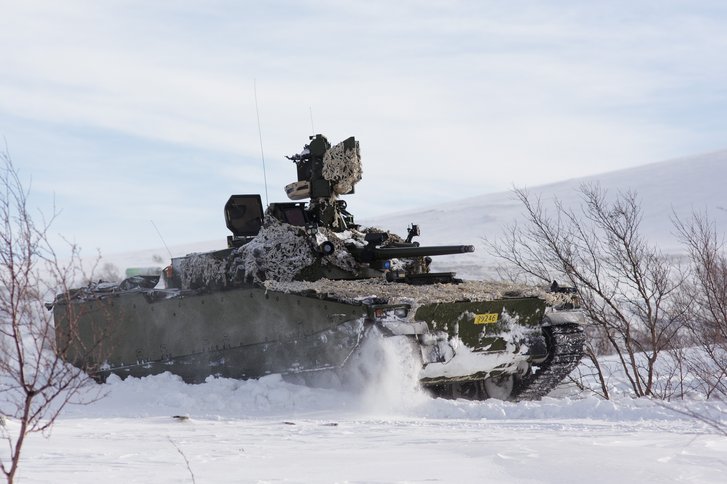
This article is aimed at presenting critical technological advantages, such as noise, vibration, weight reduction and fuel consumption / operational distance, thereby comparing composite rubber tracks (CRTs) and conventional steel tracks.
Steel tracks are obsolete
It began on the Somme battlefield on 15 September 1916 with the debut of the first iron clad tracked tank Mark I. Today, 100 years later, some are still stuck using steel tracks, regardless of the vehicle’s weight class. Throughout the world, most tracked military vehicles, like Main Battle Tanks (MBTs), use steel tracks with rubber pads. Steel tracks, however, feature several disadvantages compared with composite rubber tracks. This includes severe vibrations that have adverse effects on the health of the people inside and on the mechanical health of the vehicle and its electronic equipment, leading to more frequent breakdowns. The metal tracks are also bad for roads, since they cause considerable damage and result in substantial repair compensation claims on the part of the road authorities.
Steel tracks on combat vehicles - typical design characteristics
Track drives are used to give heavy combat vehicles sufficient off-road capability. Despite their high weights, the track drives afford such vehicles a relatively low specific ground pressure and a substantial ability to overcome obstacles, such as trenches, steps, etc.
The advantages of tracks are:
- The implementation of the best-possible off-road capability and the ability to overcome obstacles;
- Relative protection from enemy fire, particularly when using protection skirts;
- The convenient design, providing a low vehicle silhouette, and
- Good manoeuvrability in a confined space – e.g. with corresponding steering gears turning around the vertical axis is possible.
On the other hand, steel tracks have several disadvantages in other areas, such as e.g.:
- A relatively high rolling resistance;
- They are relatively expensive, especially in the LCC user phase;
- Their high vibration and the vibration load on the crew and the equipment;
- The high level of noise, especially at higher speeds.
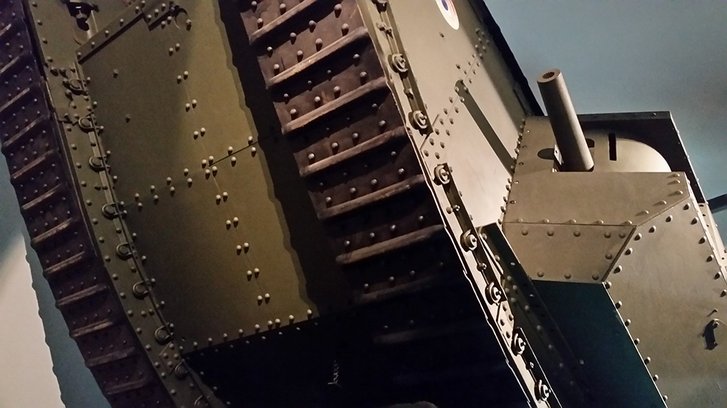
Composite Rubber Tracks (CRTs)
CRTs are up to 50% lighter than steel tracks and increase the vehicle’s performance, because they:
- offer a lower rolling resistance,
- have a reduced noise level,
- have an increased top speed,
- reduce the vibration,
- have a better traction, and
- have a lower fuel consumption.
CRTs tested on a heavy vehicle
From July to November 2016 , comparative testing took place in Canada with Leopard 1 C2 vehicles, weighing 42,000 kg each, one with CRTs and the other with legacy steel tracks. A durability trial was conducted on the vehicle with CRTs. The summary of the final report states as follows:
The aim of the testing was to compare the CRTs with the legacy steel tracks in terms of vibration, noise, rolling resistance, and to validate the durability of CRTs on a 42,000-kg vehicle platform. The weight of a CRT is 47 per cent lighter than that of a legacy steel track, therefore, the weight-saving for the tracks amounts to over 1,600 kg on the complete vehicle. The rolling resistance was measured during the testing and revealed a reduction of 50 per cent in the rolling resistance for vehicle speeds under 20 km/h and of up to 175 per cent for vehicle speeds over 20 km/h when using CRTs. This reduction would lead to fuel savings of at least 33 per cent and thus increase the operational range by 50 per cent using CRTs. The technology improvement of CRTs revealed a durability potential of 6,600 km for a 580 mm wide track mounted on a 42 ton vehicle platform.
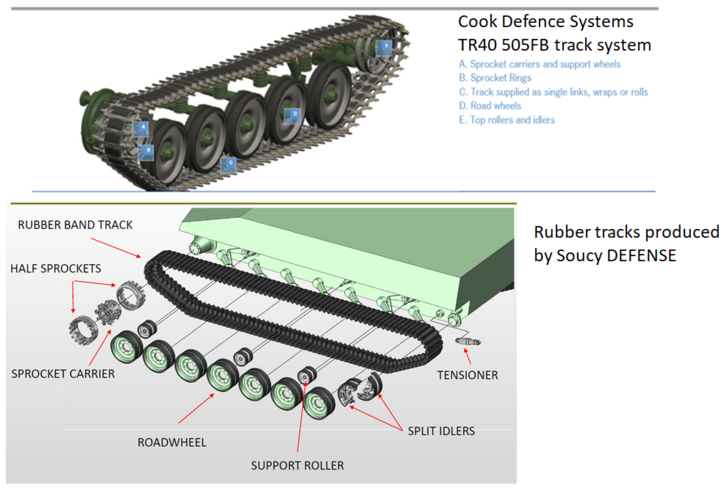
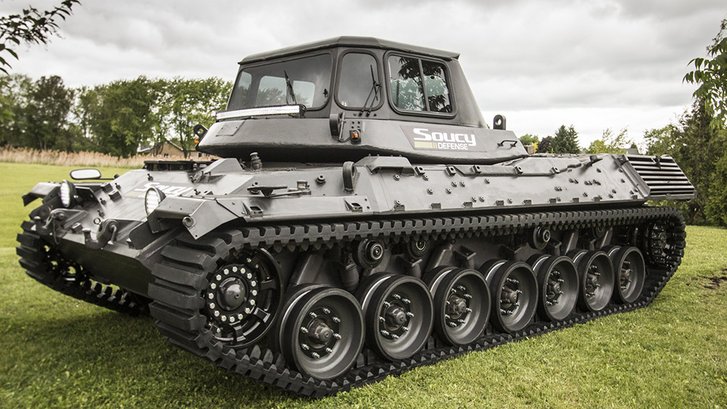
Future
At the defence and security industry trade fair Eurosatory 2014, BAE Systems presented a rubber tracked CV90 with a COCKERILL XC-8 105 HP tank cannon. Many armoured combat vehicles were also fitted with CRTs for trial purposes, including Alvis Scimitar reconnaissance vehicles, the Spartan APC, the PMMC G6 APC from FFG and the General Dynamics ASCOD APC. In the foreseeable future, combat vehicles weighing more than 30 t will be equipped with rubber track drives. Soucy DEFENSE’s Leopard 1 MBT modified platform demonstrator has proved that vehicles with a combat weight approaching 45 tons can be successfully fitted with CRTs. One example that would benefit from using CRTs is the U.S. Army's Mobile Protected Firepower Program (MPF).
The U.S. Army wants a system for the infantry brigade combat team, which offers mobility, protection and firepower. They do not expressly say that they want a light tank, they give the technical requirements in terms of how much mobility, how much protection and how much firepower are required. The Army’s requirement for the MPF’s maximum weight is to be no more than 32 tons. However, if the vehicle is intended to be airdropped, that would be far too heavy.
BAE Systems has presented the XM8 Armoured Gun System with CRTs. The XM8 was originally developed in the 1990s and intended to replace the Sheridan, before the system was cancelled. The XM8 weighs roughly 25 tons with its Level III armour package. Soucy DEFENSE CRTs are standard equipment on BAE Systems Hägglunds BvS10 and Singapore Technologies Kinetics Bronco all-terrain vehicles.
A number of countries, such as Canada and Denmark, have also fitted their fleets of BAE Systems M113 series Armoured Personnel Carriers and its variants with Soucy DEFENSE CRTs, which at the moment are extensively used in Afghanistan. The Norwegian Army and the Royal Netherlands Army are in the process of replacing steel tracks with Soucy’s CRTs.
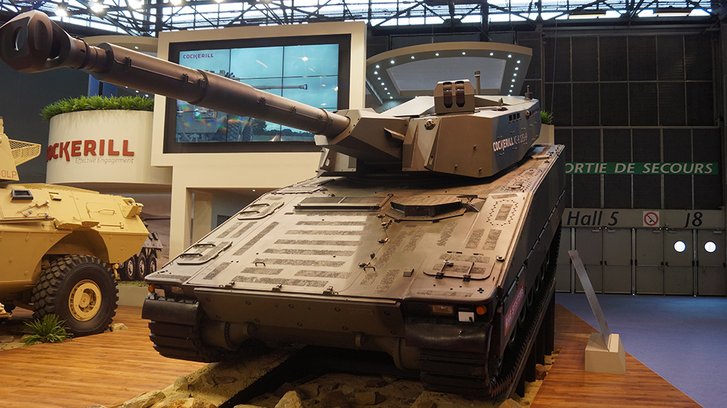
The Norwegian Army value the advantages of using CRTs
Norway has used CRTs for over ten years, both on the upgraded M113s and a few of the earlier CV90 Mk Is in Afghanistan operations. Norway’s armed forces became the forerunners in using rubber tracks on all new CV9030 Mk III versions .
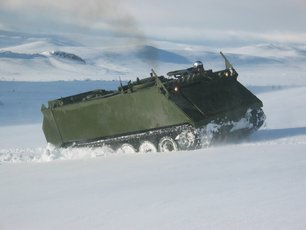
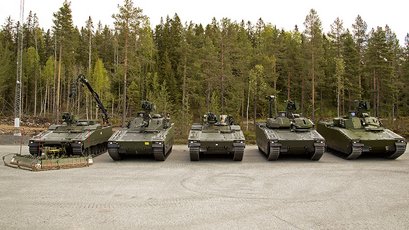
The CRTs reduce the overall acoustic signature, which for example is essential for the Reconnaissance Vehicle. (Photo: Ole-Sverre Haugli/Norwegian Armed Forces)
When experience counts
When the old infantry “riding horse” M113 was fitted with new “shoes, engines and suspension”, the new CRT “shoes” offered the user significant operational advantages . This included reduced noise and vibration as well as a 50 per cent reduction in track weight. The rubber track system is suitable for all types of ground conditions and temperatures and it is maintenance free. The vibration level in the M113 is said to be reduced by almost 70 per cent. On the CV9030 it has been confirmed by way of verification tests that the mobility is increased by using CRTs.
The lifetime of these CRTs are comparable with steel tracks. CRTs improve the mobility, especially on snow. They also provide better acceleration. One driver said: “It gives a feeling of almost like getting a few hundred horsepower extra, while fuel consumption is reduced.” CRTs generate far less noise and vibration, and thus offer better ergonometric conditions for the soldiers and the equipment inside the vehicle. Compared with iron tracks, CRTs have, as already mentioned, approx. half the weight of steel tracks, and thus reduce the vehicle’s weight by 1,200 kg. That makes it possible to enhance the armour package while maintaining the vehicle’s original weight. The internal noise is reduced by, 5-10 dBA. In addition, the risk of track throwing and dust clouds is reduced when driving.
By being maintenance free, CRTs also reduce the LCC and LSC. When it comes to the workload, the handling of a complete composite rubber track in the field is heavy. A new tool set makes it manageable.
Bradley with steel tracks are second to rubber tracked CV9030s
In addition, the newest CV90 vehicles have proved to outperform the Bradley in light snow thanks to the higher sprocket and a better angle of the track, as well as in passing over the 1.2-meter step.
Improved mobility at the tactical level – sand
When testing a combat vehicle with steel tracks vs same type vehicle with CRTs in dry sand, calculating Drawbar Pull (per cent of Gross Vehicle Weight) proves that CRTs have a better tracking performance.
Improved mobility at the tactical level – winter
When testing the M113A3 performance results / drawbar pull in winter conditions, it has shown that, on ice, steel tracks with rubber pads have an average of 4,492 lb force (lbf), while with grousers the average is 5,671 lbf. Compared to this, the M113A3 with CRTs without chains has an average of 8,616 lbf, and with chains the average is 10,863 lbf – this is a considerable improvement vis-à-vis steel tracks. When it comes to braking on ice – bringing the vehicle to a full stop from a speed of 50 km/h – the M113A3 with steel tracks and rubber pads has an average of 330 ft distance, while with grousers the average distance is 200 ft. With rubber tracks the average is 154 ft, and with chains the average distance is 116 ft – which amounts to a huge improvement over steel tracks.
APC / IFV fuel economy
Comparing APCs / IFVs with steel tracks vs those with CRTs shows that CRTs reduce the fuel consumption by at least 30 %.
Life Cycle savings
A rubber track will not stretch over time, there is no pads replacement, the sprocket and the idler will last longer, and there will be hardly any replacement of road wheels. On average, the segments of a steel track must be repaired or replaced after just 400 km (250 miles) of use. CRTs last more than 3,000 km (1,865 miles) before they need to be replaced. Metal tracks are heavy, which means a beefier suspension is needed and the vehicle also has to carry replacement tracks. Like wheeled vehicles, the rubber-tracked versions have a lower ground pressure than 8-wheeled combat vehicles and will not damage paved road, which means that there will be no costly road repairs. The reduced vibration will increase the life expectancy of electronics, ammunition and the operational availability, and together with the reduction in fuel consumption, there will be a noticeable reduction in the Life Cycle Cost.
Enhanced vehicle protection level by maintaining the original power-to-weight ratio
Replacing steel tracks with CRTs allows putting on extra protection components due to the weight saving on the track side. These components can be, among others, belly armour protection against mines / IEDs, a front glacis plate, add-on armour of different types, etc.
Mine / IED resistance – rubber band tracks
A tank mine or a heavy explosive charge / IED will tear apart tracks and drive. CRTs have some positive features, e.g. they absorb energy and do not contribute to sharp metallic objects flying around.
Battle Damage Repair (BDR) kit for CRTs
The vehicle is equipped with on-board BDR tools and a repair kit in the event of unforeseen track breakage. The vehicle will be back in battle within 30 minutes or it can limp home within a range of 130 km.
Summary
Generally, CRTs are up to 50 per cent lighter than steel tracks and reduce the rolling resistance, the vibration and the noise level. Reduced noise improves the interoperable communication. Trials have shown that a noise reduction of up to 13.5 dB can be achieved, while a reduction in vibration of up to 70 per cent is possible by fitting CRTs.
The combination of lighter CRTs and a reduced rolling resistance results in a higher power-to-weight ratio and, at the same time, increases speed, mobility and manoeuvrability. CRTs do not cause damage to paved roads and are, therefore, modular / interchangeable in the vehicle’s mission role (adaptability). Using CRTs reduces the cost per unit out of the factory, as compared with steel tracks; the CRTs will double the track life in terms of durability. Moreover, 20-25 per cent saving in reduced repair / maintenance costs and up to 40 per cent fuel reduction – thus increasing mission range – and a reduced Life Cycle Cost can be expected.
CRTs lower the gross weight and can make it easier for a vehicle to be transported within the weight class and they increase the Air Born Capability, or otherwise the gain in weight saving may be used to increase the load bearing capacity, e.g. to increase the armour protection. Against blast / IED explosion, CRTs do not give a secondary effect, except that rubber to some extent absorbs energy. Small arms fire has no impact on CRTs. CRTs are recyclable with environmental control systems.
Conclusion
Compared to steel tracks, CRTs provide more traction, in part because they are lighter, but also because they can be made wider than steel tracks, which reduces the ground pressure and tracking. This means that vehicles fitted with them do not get stuck easily in the mud. The vehicles accelerate faster, too, and drivers say the handling is almost as good as on paved roads and with wheeled vehicles. On top of that, the vibration level is quite low and the vehicles are quieter. The LCC is also particularly low.
The weight saving owed to the use of CRTs is over 1,600 kg for the vehicle due to the track weight being 47 per cent lighter than that of legacy steel tracks. The rolling resistance is greatly reduced with CRTs as well, with measurements revealing a 50 per cent reduction for CRTs at vehicle speeds under 20 km/h and up to 175 per cent at vehicle speeds over 20 km/h. This reduction leads to a minimum fuel saving of 33 per cent and a 50 per cent increase in the vehicle operational range for using CRTs.
The Canada trials also show that the improved technology of CRTs offers track durability of approximately 6,600 km for a 580 mm wide track used on a 42,000 kg Leopard 1 C2 vehicle.
About the author
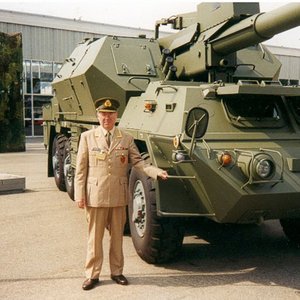
Major (P) Walter Christian Håland (pictured standing beside the armoured self-propelled howitzer system ZUZANA) has completed artillery courses in Norway and the UK. He has served in the Norwegian field artillery for many years. He served as a UN officer in Lebanon from 1979 to 1980. Before retirement, he served two years as a Lieutenant Colonel in the Material Branch, HQ DEFENCE COMMAND NORWAY. He is a member of the European Military Press Association